In ancient Egypt, artisans beat and stretched gold into gold leaf, and
put it on stones, bones, etc., to make crafts or sacrifices. In the
above process, the edges of the gold foil are easy to break and fall
off, resulting in some gold fragments. Later, craftsmen discovered that
mixing these debris with natural oils and coating them on these objects
can also achieve a decorative effect. Soon these discoveries and
technologies were transferred to silver. Over time, this technology was
also transferred to ancient India, China, and later to Europe. With the
development of metal smelting technology, metallic aluminum appeared. It
was found that aluminum is relatively soft in texture and has good
ductility, that is, it can be rolled into flakes by pressure. This is a
very important prerequisite for the production of aluminum pigments.
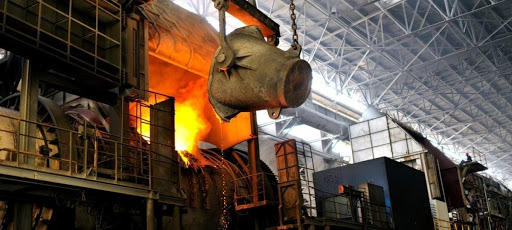
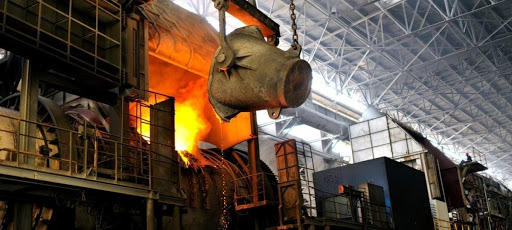
During the Renaissance in Europe, aluminum pigments were produced by
mechanical ramming. Even using a rigid hammer, hammer the aluminum block
on the steel plate into a sheet. During processing, grease is used as a
lubricant. However, the efficiency of this process is not high, there
is a danger of explosion, and the performance of the product is not
satisfactory.
In 1892, the German Schlenk Company began to produce aluminum powder.
In 1910, Alcoa began producing aluminum pigments for coatings.
In 1930, Professor E.J.HALL of Columbia University in the United States
invented the wet grinding process for the production of aluminum
pigments. The method is to use a roller ball mill to add a certain
amount of steel balls, granular aluminum, solvents and fatty acids. Turn
on the ball mill and grind at a certain speed. Using the impact and
shear force generated by the movement of the steel ball, the aluminum
powder is first stretched into flakes, and then crushed to a certain
degree of fineness (particle size). Due to the presence of solvents,
aluminum is isolated from contact with oxygen in the air, thereby
playing a protective role and avoiding explosion hazards. At the same
time, the output and quality of products have been greatly improved.
Therefore, wet ball milling has gradually become a metal pigment. The
main preparation process. Up to now, the world's major metal pigment
manufacturers have adopted this process.
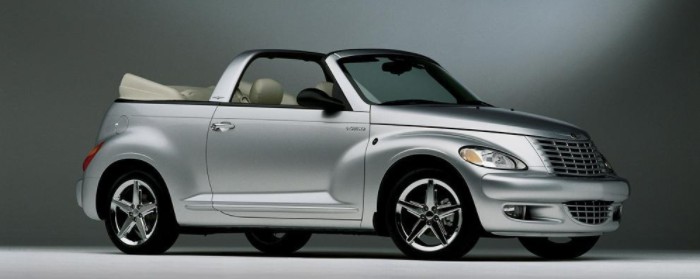
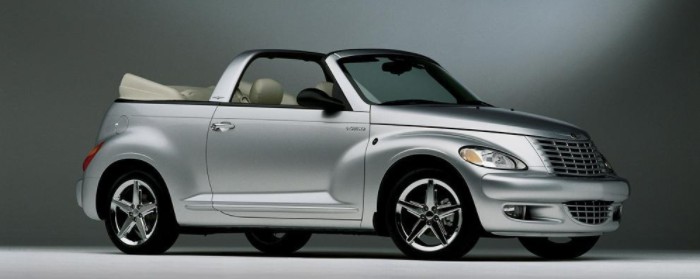
In 1934, since the Chrysler Automobile Company of the United States
first used aluminum pigments in automobile coatings, the technology and
output of metallic pigments have been greatly improved. At present, with
the advancement of metallic pigment technology, more than 50% of
automobiles in the world are painted with metallic flash paint. Among
them, more than 75% in the United States and more than 50% in Japan and
Europe contain aluminum pigments. For household and office appliances
such as televisions, computers, refrigerators, and mobile phones,
aluminum pigments are used in a larger proportion and become a trend.
From magnificent ancient palaces to modern high-rise buildings, from
cars on the streets to people’s daily necessities, products with
metallic luster can be seen everywhere, but many products with metallic
luster are not real metal products. The emergence of metallic paint
(aluminum pigment occupies a large proportion of metallic pigments) has
made up for the lack of people's pursuit of metallic luster, which not
only reduces the cost, but also meets the demand. Solvent-based metallic
paint has excellent luster and excellent weather resistance. ,
Corrosion resistance, widely used in industries such as automobiles,
motorcycles, bicycles, ships, toys, home appliances, computers and
mobile phones. Therefore, under the impetus of the market, the
development of aluminum pigments is unstoppable, and the market prospect
is very broad.