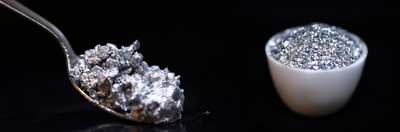
①Direct grinding: Add dispersant and antioxidant to the aluminum powder
raw material, and then use water-soluble solvent to grind directly in
the ball mill. Advantages and low cost. Disadvantages: The production
process is dangerous and the effect is average. For example: poor
corrosion resistance, unstable, etc.
② Replacement by oily silver paste is also called oil-to-water
replacement. Use high-boiling water-soluble solvents (such as ethylene
glycol butyl ether) to replace the mineral spirits by distillation, and
add some dispersants and antioxidants.
Advantages: A good metallic appearance of aluminum silver paste can be
obtained. Disadvantages: poor corrosion resistance, unstable, poor
versatility. The first two are only low-end primary products that rely
on some high-molecular materials to physically adsorb on the surface of
the silver paste to prevent the erosion of some water and impurities.
③Compared with the first two, the universal method that is recognized
internationally and has a better effect is to coat the surface of the
aluminum powder with surface silica (also called nano-silica surface
deposition coating). Covered with a dense protective film with a
thickness of 50-100 nanometers, which adsorbs the deposited film of
nano-silica particles on the surface of aluminum powder through a
chemical reaction to prevent corrosive substances such as water, acid
radical ions, alkaline ions, oxidants, etc. erosion. Advantages: get
better results, higher acid and alkali resistance, and stability.
Disadvantages: high cost. To carry out degreasing, and the chemical
reaction operation of silica deposition coating. In addition, chemical
equipment such as reactors is also used. The diameter of the nano-silica
particles is about 10-30 nanometers. The better the reaction control,
the smaller and uniform the nano-particles, and the denser the
protective film made, and the better the effect.
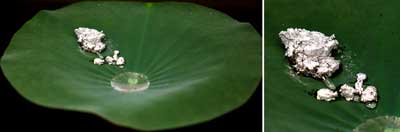
For example: Taking the high-end water-based aluminum silver paste
produced by our group as an example, in order to obtain the best overall
effect, the coating film as a whole is roughly divided into a
three-layer film structure. Bottom layer: Passivation film structure,
which has the effect of pretreatment and surface activation.
Intermediate layer: the key dense film structure of nano-silica. Surface
layer: surface modification of polymer organic materials for better
dispersion, leveling, and orientation.
On this basis, different directional arrangement effects such as
floating silver, immersed silver and suspension can also be obtained
through different modification methods.
2. How to test the difference between water-based aluminum and silver
paste? That is, how to identify the advantages and disadvantages of
water-based aluminum silver paste, such as: corrosion resistance, etc.,
to prevent bad businesses from shoddy. This requires alkali resistance
testing. Reason: For water-based paints and water-based paints, their
systems are weakly alkaline, because normal polymer resins are
lipophilic, so making water-based is the process of changing resin oil
to water. It needs to be hydrophilic. In order to achieve this, it is
necessary to graft hydrophilic hydroxyl, amino or carboxyl groups on the
polymer material. This type of modified group is alkaline, so the resin
produced is generally weakly alkaline, so we need to conduct an
alkaline resistance test.
Quick test: Directly perform the strong alkali resistance test. First,
configure the test solution: 1.2% sodium hydroxide solution, pH value
between 14 ± 0.1, and temperature maintained at about 25 ℃.
Reaction equation: 2H2O+2Al+2NaOH==2NaAlO2+3H2
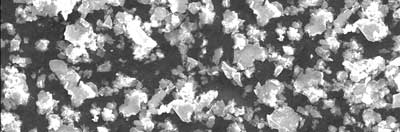
Then, about 2 grams of water-based aluminum silver paste was diluted
with 4 grams of clean water and then poured into 100 ml of test solution
to test the length of time it can stabilize in the test solution. This
method can directly distinguish whether the production process is
oil-to-water or direct grinding, or high-end silica-coated water-based
aluminum silver paste. If it is not covered with a silicon dioxide film,
it will usually start to react within 1 minute, the reaction is
violent, and it will generate a lot of gas and generate heat. If it is
coated with silica, it can be stable for about 3 minutes if it is poor
in China, and it can be stable for 5 minutes to 20 minutes.
If the stabilization time can reach more than half an hour, the alkali
resistance effect obtained will be even better. For now, the benchmark
product in the water-based silver paste market is the water-based
aluminum silver paste produced by the German Aika Company. Its products
can generally get a stable time of about one hour when tested in the
test solution. In addition, the aqueous aluminum silver paste coated
with silica can generally be used in summer. On the contrary, the
water-based aluminum-silver paste processed by other processes will have
adverse reactions such as heat generation and flatulence during
transportation in summer. If the test stability can reach more than half
an hour, the storage period can reach 1-2 years. For products that take
less than half an hour, the shelf life is only three months to six
months. Of course, the degree of alkalinity (pH level) in the
water-based paint and the water-based paint itself also has a certain
impact on the storage period.