The technology of aluminum pigments is still in continuous progress.
Its current technical development focuses mainly on water-based and
coating modification. In addition, it improves pigment fineness, shape
regularity, particle size uniformity, product quality stability and
other physical properties. Indicators, improvement of pigment dispersion
and other properties, research and development of color aluminum
pigments, special functional aluminum pigments, etc. are also its
technological development trends.
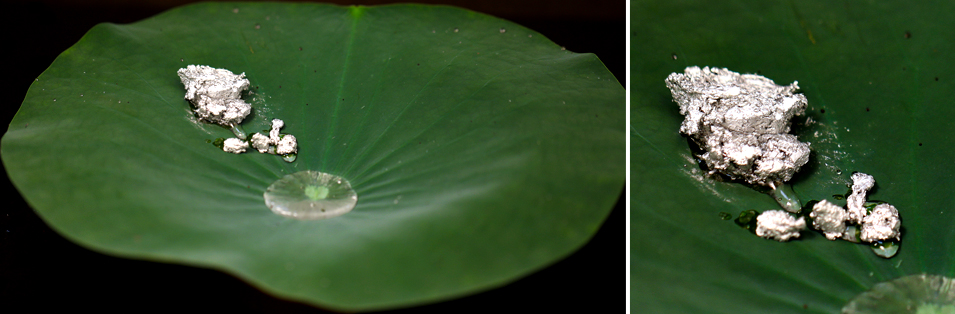
1. Water-based product (water-based aluminum pigment)
Untreated aluminum pigments will chemically react with water to produce
a large amount of hydrogen, which will destroy the metallic luster of
aluminum particles, which will seriously affect their weather
resistance. Therefore, the quality of water-based aluminum pigments and
their application fields and production processes, especially coatings
The process is closely related. The organically treated products have
good water resistance, very low gas release and excellent weather
resistance; the inorganically treated products have a thinner coating
layer, which can effectively display the metallic luster of aluminum
pigments. Water-based aluminum pigments are one of the inevitable
development directions of the aluminum pigment industry. Although
international companies have nearly 60 years of experience in this
field, the research and development of new products has not stopped.
2. Low pollution in production process
In addition to water-based aluminum pigments, domestic companies also
need to develop production processes towards low pollution. Many
domestic enterprises used 200# solvent oil for grinding before 2009, and
used high-boiling trimethylbenzene and tetramethylbenzene as the final
solvent of aluminum silver paste. The aromatic hydrocarbons contained in
these solvents are especially high-boiling trimethylbenzene and
polycyclic tetramethylbenzene. Aromatic hydrocarbons are harmful to the
human body and the EU has banned them by legislation. At present, most
companies have adopted alkane solvents, such as high boiling point
dearomatized hydrocarbon solvents D60, D70, and D80. However, the
storage stability of aluminum pigment products and the compatibility of
coatings still need to be improved, and a certain proportion of
assistance is often required. Solvent.
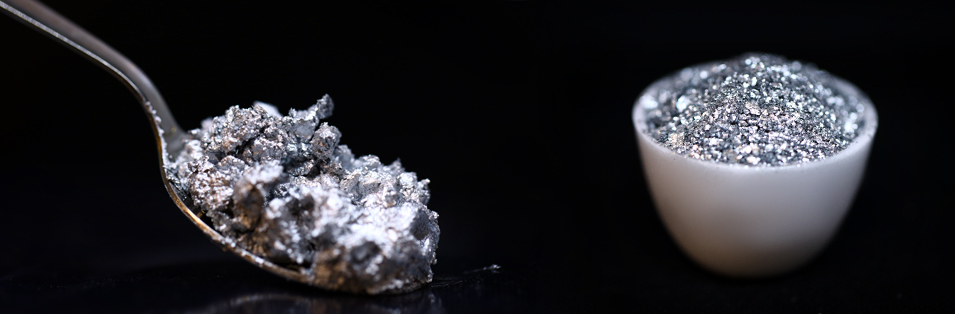
3. Colorization of aluminum pigments
Another development trend of aluminum pigments is to form color effect
aluminum pigments through surface coating modification. Color aluminum
pigments not only have the original metallic luster of aluminum
pigments, but also have bright colors. Because the color aluminum
pigment has bright colors, strong corrosion resistance, good insulation,
not easy to fade, and strong metallic luster, it has a wide range of
application development prospects.
In 2010, BASF launched a new generation of
PaliocromBrilliantOrangeL2850 color aluminum pigments, which can display
color effects from orange to red. The product uses SiO2 and iron oxide
coated aluminum flakes, which contain 40% to 60% aluminum and 25% to
45%. Naphtha, 10% to 20% iron oxide and 1% to 5% silicon dioxide. The
product has a good flashing effect and high hiding power, and is
suitable for solvent-based and water-based systems. It is mainly used
for high-performance automotive coatings and industrial coatings for
consumer electronic products such as computers and mobile phones. It can
also display more abundant effects together with other effect pigments.
Color effect The coating process of SiO2 and organic pigments can
improve the chargeability of aluminum pigments. Colored aluminum
pigments are also suitable for powder coatings produced by the dry
blending process, but they are not suitable for the current bonding
process, because this process easily causes a large amount of colored
pigments to detach from the surface of the aluminum particles, thereby
causing the loss of specific optical properties.
4. Special functional aluminum pigments
It is the consensus of the industry to continuously expand the
application fields of aluminum pigments. At the end of 2007, Aika
launched an aluminum pigment for laser marking. Laser marking technology
is one of the largest application areas of laser processing. It uses
high-energy-density laser to locally irradiate the workpiece to vaporize
the surface material or cause a chemical reaction of color change,
thereby marking various characters, symbols and patterns. Aika’s
Lasersafe040 aluminum pigment product is a pigment concentrate that can
be used for thermoplastic polyolefins, such as PVC, PET, TPU, and
polycarbonate. The addition amount is only 0.01%, which is very suitable
for YAG laser (yttrium aluminum pomegranate). Stone laser) high-speed
assembly line production, with high-contrast effect, can depict
crystal-like patterns, text, and even photos in the plastic. Unlike
other pigments used for laser marking, this pigment does not contain
heavy metals, so it complies with FDA and European food safety standards
and other regulations, and can be used in many fields such as food
packaging.
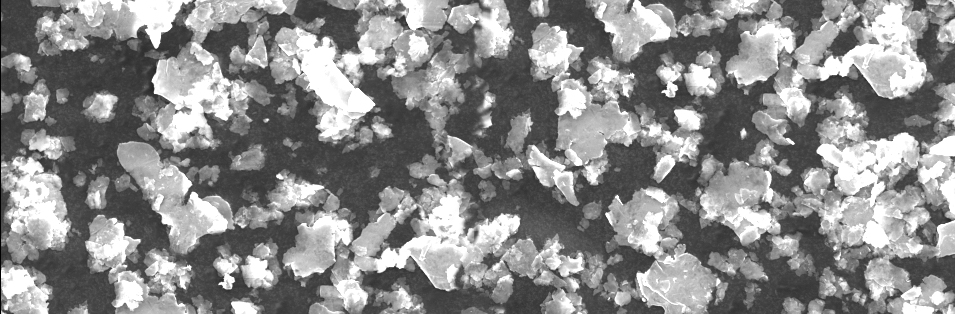
5. Nano aluminum pigment
Nano-flaky aluminum pigments have attracted more and more attention in
recent years. Their diameter and thickness are in the range of
nanomaterials (30-50nm), so the diameter-to-thickness ratio is much
larger than traditional aluminum powder. It has a very strong
reflectivity to light and can be evenly distributed in the paint And it
is almost horizontally distributed, and the protective and decorative
effects produced are significantly better than traditional aluminum
pigments. The current nano-flaky aluminum powder pigments mainly refer
to the aluminum pigments (ie electroplated aluminum pigments) produced
by the physical vapor deposition method (VMPs) process, such as
evaporation-condensation method and sputtering-deposition method, while
laser-induction heating method, Plasma heating method, electron beam
radiation method and other nano aluminum powder production processes are
still in the laboratory stage and have not been industrialized.
6. Improve stability, dispersion and alignment
The stability, dispersion and orientation properties of aluminum
pigments are of great significance to their application effects.
Aluminum is an active metal. In order to improve its stability, it is
often necessary to use an inorganic layer or an organic layer for
coating modification. The coated aluminum pigment can also improve the
shear resistance performance and keep the shape of the scales from being
damaged, which is particularly important in application fields such as
powder coatings and plastics. In addition, the aluminum particles have a
large specific surface area, and the aluminum particles without surface
treatment are easy to agglomerate, and the coated aluminum pigment has
better dispersibility.
Finally, in terms of technology, Chinese aluminum pigment companies
also need to strengthen the research on fatty acids and various
additives used in the production of aluminum pigments to meet the
requirements for the production of high-end aluminum pigments.
Sunflower Aluminum Pigment
Sunflower water-based aluminum paste
Sunflower aluminum paste
Aluminum paste producer
Aluminum powder producer